Lithium-ion batteries are a helpful technology used to transition us away from fossil fuels by electrifying transportation and supporting renewable energy sources. The batteries contain minerals that can be recovered for use in future batteries, including lithium, cobalt, nickel, copper, aluminum, and graphite.
Sourcing materials from recycling is more sustainable than mining virgin materials, and in some cases, it’s the only viable domestic option for the United States (US) where most battery materials or the batteries themselves are imported. However, minerals aren’t always recovered at high rates during recycling, either because the best available technology isn’t used or because low or volatile mineral prices make the recovery of some minerals uneconomical for recyclers. This means that these minerals are effectively lost from the supply chain when they otherwise would have been a valuable resource.
But, there is a solution. Setting required mineral recovery rates ensures that a high percentage of minerals from retired batteries goes back into the US economy and decreases mining needs. When partnered with a policy that requires producers to recycle batteries in the US, recycling companies aren’t subject to the volatility of global mineral prices.
Without this type of policy, mineral recovery rates could suffer during price drops, therefore forgoing an opportunity to develop a lower-impact domestic supply chain of battery materials to help sustain continued growth in the US battery manufacturing sector. Take, for example, the aluminum scrap market, which is continually impacted by fluctuating prices that result in lower recycling rates. Aluminum recycling is currently at a 30-year low, down to only a 43% recycling rate. While aluminum operates differently than the retired battery market (black mass), the root of the cause is the same – market volatility hurts recovery rates.
The European Union is starting to address this issue. In 2023 they created a comprehensive battery policy that includes mandatory mineral recovery rates. They just released guidelines for calculating and verifying recycling efficiency and recovery of materials from waste batteries. Since the European Union is the leader for this type of policy, the United States can learn from their approach and similarly ensure:
- Reduced amount of mining needed for vehicle electrification;
- high mineral recovery and mineral production in the United States to maximize benefits; and
- US recycling companies are supported during times of fluctuating mineral prices, and technology and domestic mineral production doesn’t lag behind other regions.
What are the European Union mineral recovery rate requirements?
A recovery rate is the amount of a mineral that is recovered in a usable form compared to the total amount in the waste batteries that were recycled. While batteries contain a handful of minerals, the European Union has only set requirements for lithium, nickel, cobalt, and copper because of the increasing demand for clean technology and the reliance on imports of these minerals.
The requirements increase over time; the mineral recovery requirements are 90% for cobalt, copper, and nickel and 50% for lithium by 2028. They increase to 95% for cobalt, copper, and nickel and 80% for lithium by 2032. Lithium recovery requirements are lower than the other minerals because not all facilities and processes recover the mineral today, therefore these requirements may require ramping up that capability.
Importantly, these requirements do not exceed technological feasibility. For example, researchers recently analyzed data from Redwood Materials, a leading battery recycler in the US, and found they can recover well above these levels in their recent Nature article.
How are mineral recovery rates calculated?
The most effective recycling policies contain recovery rate requirements but including them means each facility needs to have a standard way of calculating to ensure compliance. The European Commission recently resolved this problem by releasing guidance on how each facility should calculate and verify the recovery rates. The United States is exploring how to ensure mineral recovery through recovery rates, and this approach could be applied to the recycling policy under development.
The recovery rates of each mineral are calculated yearly and consider the minerals contained in the battery or black mass going into each step of the recycling process, and then the output of materials that can then be used to manufacture new products.

Finding the mineral output is straightforward and is something recyclers already do since they are looking to resell the minerals they recover. Determining the mineral input, however, is not as simple as it seems but is also crucial. This is because there is an array of battery chemistries and the batteries are not always labeled, so recyclers may not know the exact makeup of the batch they are processing. Luckily, this is something that can be addressed with required labels in the battery recycling policy itself.
The guidelines recommend conducting a sorting analysis of the input materials by continuous or representative sampling. The recyclers can do this by one of the following:
- labels or an online database (if available) to determine battery chemistry;
- sampling and analyzing the composition of batteries or black mass entering the waste stream; or
- determine the composition of all the output minerals plus emissions and waste resulting from treatment.
How would recovery rates impact US recycled content?
Minimum mineral recovery rates will help ensure that future mining is offset by recycled content. If we look at lithium, a mineral that is not always recovered, the amount recovered vastly impacts the percent of demand that can be met with recovered lithium and the demand for newly mined minerals.
Our analysis for lithium shows how recovery rates dramatically impact future mining needs With recycling processes achieving a 90% lithium recovery rate, almost 60% of lithium demand can be met with recycled content in 2050, equaling almost five hundred thousand metric tons from 2025 to 2030, or enough for fifty four million average EVs[1]. Alternatively, lower recovery rates increase mining requirements. A 50% recovery rate would require an additional two hundred and ten thousand metric tons of newly mined lithium compared to the use of a 90% recovery rate. And a 25% recovery would require about three hundred and forty metric tons more newly mined lithium. However, these would all be improvements from the status quo; at present, there is no required recovery rate for recycling and, therefore, in many cases, no recovery of lithium.
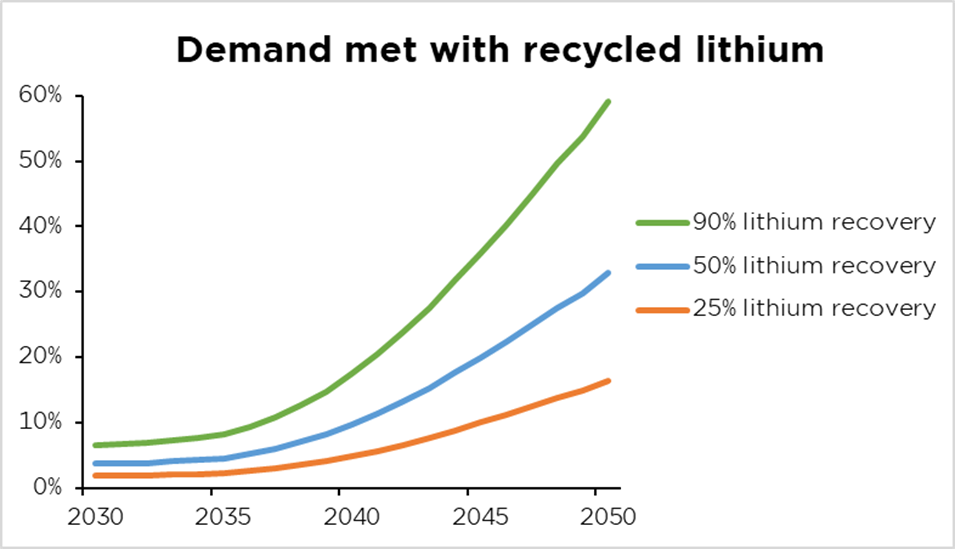
This calculation only includes US passenger vehicle lithium demand and is based on the analysis of Dunn et al. (2025). Additional recovery rates have been applied to the Ambitious Reduction Strategy to get these results.
Mineral recovery is essential to creating a lower-impact and resilient supply chain
Mineral recovery rate requirements are an essential part of creating a secondary mineral supply chain and circular economy for lithium. While mineral recovery rates have not yet made it into battery recycling policy in the United States, we can look to folks across the pond to learn how to create and measure this type of standard.
Appendix: How the EU wrote recovery rates into law
Including recovery rates in battery recycling policy doesn’t need to be complicated. The EU legislative text below helps illustrate how other policy makers could go about implementing recovery rates in their jurisdictions.
REGULATION (EU) 2023/1542 OF THE EUROPEAN PARLIAMENT AND OF THE COUNCIL– mineral recovery rates for lithium-ion batteries
By 31 December 2027, all recycling shall achieve at least the following targets for the recovery of materials:
(a) 90 % for cobalt;
(b) 90 % for copper;
(c) 50 % for lithium;
(d) 90 % for nickel.
By 31 December 2031, all recycling shall achieve at least the following targets for recovery of materials:
(a) 95 % for cobalt;
(b) 95 % for copper;
(c) 80 % for lithium;
(d) 95 % for nickel.
Supplementing regulation – mineral recovery rate calculation and verification
[some language has been taken verbatim and has been modified to clarify and condense]
Input fraction: the mass of waste batteries entering the waste battery recycling process, waste anode and cathode active materials, current collectors, and electrolyte salts. Recyclers shall determine the share of different waste battery chemistries present in an input fraction by conducting a sorting analysis of the fractions by continuous or representative sampling. This can be done using one of the following methods:
- on the basis of information provided by the battery producers, where that information is available on a label or in an electronic record;
- by determining the chemical composition of all the output fractions plus emissions and waste resulting from treatment;
- by sampling and analyzing the input fraction.
Intermediate fraction: the mass of waste batteries when it is neither input nor output fraction but destined for subsequent steps in the recycling process that have the aim of converting intermediate fractions into output fractions.
Output fraction: the mass of waste batteries obtained from the recycling process derived from input fractions and converted into materials, substances, or products that can substitute primary materials, substances, or products in industrial processes of manufacturing. Metals such as lithium contained in the slag are not taken into account in calculating the rate of recovery of materials.
The mineral recovery rate shall be calculated on the basis of the chemical composition of the input and output fractions using the following equation:

Where:
TM = the target materials; either lithium, nickel, cobalt, or copper
rRM = calculated rate of recovery of materials from waste batteries in relation to a recycling process [in mass %]
mTM, output = the mass of the target material in output fractions taken into account in the rate of recovery of materials, namely the mass of TM contained in the output fractions per calendar year
mTM, input = the mass of the target material in the input fraction, namely the yearly average mass of TM contained in the input fractions per calendar year
Additional requirements addressed by the regulation:
- The recovered material shall have a TM content as high as technically feasible while avoiding excessive costs.
- In some cases, multiple recyclers may be involved in this process that also process intermediate fractions. Where a waste battery recycling process is carried out at more than one permitted facility, the first recycler shall be responsible for collecting and providing the information required.
[1] Assuming an 80kWh battery and .11 kg/kWh of lithium